Introduction
Quality Control
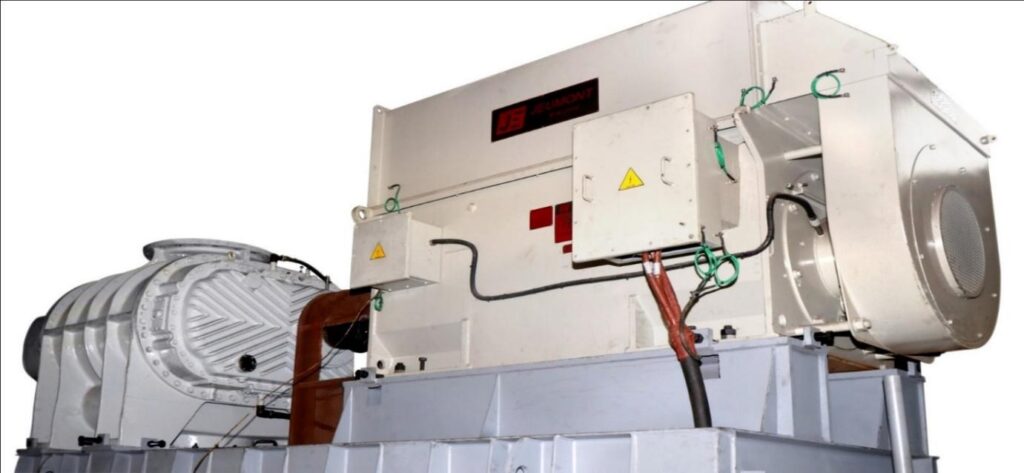
- All Testing are done as per International Standards BS1571(Part II).
- SWAM has large in-house testing facilities i.e. Test beds with test motors upto 1000KW with voltage range of 415V, 690V, 3300V & 6600V.
- Every SWAM product has to pass through a vigorous performance test.
- Each machine before dispatch has to under go continuous running i.e. Mechanical Run Test (Including check of all parameters i.e. Pumping Capacity, Temperature Rise, Vibrations, Noise Level etc.) at different set points for atleast 2-3 hrs continuously.
Many years ago Quality Control was something like “Measure twice and cut once” Today it is far more sophisticated, with automated machinery and 100% repeatability.
Emphasis on quantity and performance is a commitment of every individual at SWAM beginning at grass root level.
The quality control is practiced at all levels of the organization and all its aspects an thoroughly complied with the specified structured standard specification till the products is delivered. A new way of saying this is “garbage in garbage out”.
Swam has developed a very high level of Quality control. Not only do we check all of the raw material and castings when they are delivered. With all defects quarantined, and returned back to the supplier or sub-contractor.
In order to maintain consistency, Swam insists all final machining is completed on CNC Machines. Swam also has fixed stage measuring and testing stations, to ensure that only tested and cleared products move on to the next stage of the manufacturing process. Swam has a detailed in process inspection at various stages to ensure that final product is of highest quality and have over 18 quality control engineer during the work
Final product testing is completed at our “Hot run” testing station.
Here every finished product is run tested for between 4 to 6 continues hrs.
This test is carried out in accordance to the client’s performance specification.
At the completion of this test a test certificate is issued.
If required this test can also be witnessed by a third party.
After this the product is sent to the paint shop for its final coat.